Bao bì đóng vai trò quan trọng trong việc đảm bảo an toàn, chất lượng và thời hạn sử dụng của sản phẩm, đặc biệt là trong ngành thực phẩm và dược phẩm. Nhiều loại túi đóng gói khác nhau, chẳng hạn như túi hình gối, túi phẳng và túi tự hỗ trợ, được sử dụng rộng rãi, mỗi loại đều có những ưu điểm riêng biệt về chất lượng niêm phong, tính thẩm mỹ và tính phù hợp với các loại sản phẩm cụ thể. Trong số nhiều phương pháp, bao bì chân không nổi bật nhờ khả năng kéo dài thời hạn sử dụng của sản phẩm bằng cách làm chậm quá trình oxy hóa, ức chế sự phát triển của vi khuẩn và giúp việc lưu trữ hiệu quả hơn. Máy đóng gói chân không, đặc biệt là loại một buồng và hai buồng, rất cần thiết để tự động hóa các quy trình hút chân không, niêm phong và thổi phồng, đảm bảo tính toàn vẹn của sản phẩm và cải thiện hiệu quả đóng gói tổng thể.
Các loại túi đóng gói
Túi màng nhựa thông dụng có các dạng sau:
Túi hình gối. Phương pháp may chung là chồng đường may dọc lên nhau rồi may kín hai đầu lại như hình (1).
Túi phẳng. Có thể chia thành túi hàn ba cạnh Hình (2) và túi hàn bốn cạnh Hình (3).
Túi đứng. Các loại túi phổ biến là túi góc nhọn Hình (4), túi tam giác Hình (5) và túi cột khối Hình (6).
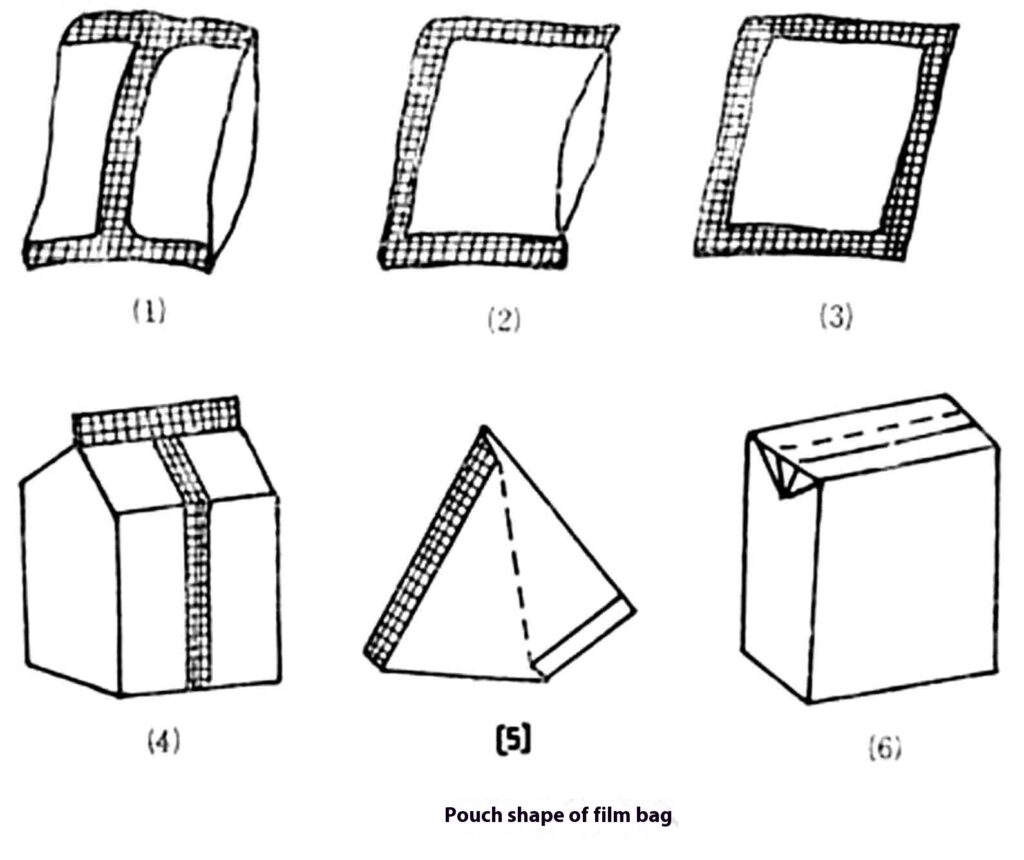
Trong quá trình làm túi, thông thường trước tiên là hàn theo chiều dọc rồi mới hàn theo chiều ngang. Do đó, trong toàn bộ chiều dài của các đường nối hàn chồng lên nhau và ghép mộng của túi hình gối, ba hoặc bốn lớp màng chồng lên nhau tại phần hàn, có tác động nhất định đến chất lượng hàn. Số lớp màng trong toàn bộ chiều dài của đường nối hàn của túi hàn ba mặt phẳng là bằng nhau, chất lượng hàn tốt hơn, nhưng hình dạng túi không đối xứng và tính thẩm mỹ kém hơn một chút. Hàn bốn mặt khắc phục được những nhược điểm của hai tình huống trên, nhưng sử dụng nhiều vật liệu đóng gói hơn và thường được sử dụng cho các máy hàn đơn giản cho các gói nhỏ. Các loại túi tự hỗ trợ có vẻ ngoài đẹp mắt và ưu điểm là tự hỗ trợ, thuận tiện cho quá trình đóng gói tiếp theo và sắp xếp, trưng bày sản phẩm. Tuy nhiên, chúng có yêu cầu cao về vật liệu đóng gói và nên sử dụng vật liệu đóng gói tổng hợp.
Máy đóng gói chân không
Đóng gói chân không là đưa thực phẩm vào hộp đựng, loại bỏ không khí trong hộp, đạt đến độ chân không nhất định, sau đó niêm phong và đóng gói. Đây là phương pháp đóng gói mới đã phát triển nhanh chóng trong ngành thực phẩm và dược phẩm trong và ngoài nước trong những năm gần đây. Nó có những đặc điểm sau:
(1) Làm chậm quá trình oxy hóa và hư hỏng, ức chế sự sinh sản của vi khuẩn, do đó kéo dài thời hạn sử dụng của thực phẩm. Thực phẩm bám vào một số lượng vi sinh vật nhất định, chúng sinh sản trong không khí và làm cho thực phẩm bị hỏng. Sau khi không khí bị loại bỏ, vi sinh vật ức chế sự sinh sản trong điều kiện không có oxy, và nhiều chất dễ bị oxy hóa cũng bị oxy hóa chậm do thiếu oxy.
(2) Thuận lợi cho hoạt động tiệt trùng nhiệt. Nếu có nhiều không khí trong hộp đựng thực phẩm, dẫn nhiệt kém, thực phẩm mất nhiều thời gian để làm nóng, thời gian tiệt trùng kéo dài; sau khi loại bỏ không khí, thực phẩm nhanh chóng tăng lên đến nhiệt độ cần thiết. Ngoài ra, loại bỏ không khí cũng có thể ngăn ngừa hộp đựng bị vỡ do giãn nở khí trong quá trình gia nhiệt và tiệt trùng.
(3) Sau khi loại bỏ không khí, thể tích được giảm xuống, thuận tiện cho việc lưu trữ và vận chuyển.
(4) Vì thực phẩm đóng gói cần duy trì một lượng ẩm nhất định và vật liệu đóng gói cũng có độ thoáng khí nhất định nên bao bì chân không không thể đạt được độ chân không hoàn toàn và độ chân không cao nhất có thể đạt tới -0,096~0,099MPa.
Nguyên lý cấu trúc của máy đóng gói chân không một buồng
Hình vẽ thể hiện cấu tạo và nguyên lý hoạt động của máy đóng gói chân không cỡ trung, được sử dụng rộng rãi trong các nhà máy chế biến thực phẩm vừa và nhỏ.
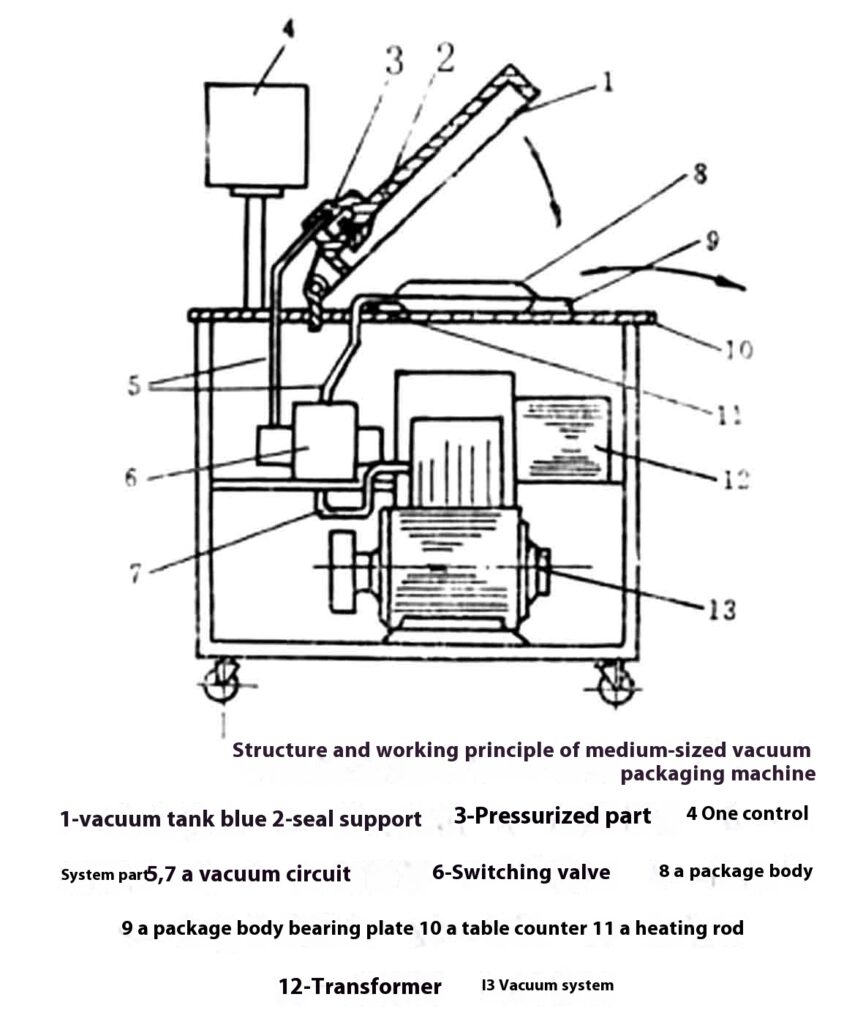
Quy trình đóng gói thực phẩm đóng túi là: đặt thân bao bì vào bể chân không để định hướng, đặt miệng túi lên khối gia nhiệt, đưa vòi hút chân không vào miệng túi và ấn nắp bể chân không xuống. Sau đó, công tắc giới hạn và rơle sẽ tự động điều khiển quá trình hút chân không, ép nóng và niêm phong, tắt nguồn làm mát, mở tự động và các quy trình khác. Mức độ hút chân không, thời gian, thời gian niêm phong nhiệt, thời gian làm mát, v.v. phải được kiểm tra và điều chỉnh trước.
Quy trình làm việc của máy đóng gói chân không nhỏ cũng giống như máy đóng gói chân không nhỏ, ngoại trừ mỗi quy trình đều được điều khiển thủ công.
Phương pháp gia nhiệt để ép nóng niêm phong thường áp dụng phương pháp gia nhiệt xung. Bộ phận gia nhiệt của nó sử dụng dây điện trở thấp và điện áp khoảng 10-50V. Khi có dòng điện mạnh đi qua, bộ phận gia nhiệt dây sẽ ngay lập tức tạo ra nhiệt và truyền đến khối gia nhiệt, sau đó miệng túi được ép nóng và niêm phong. Phương pháp làm mát niêm phong có thể là làm mát tự nhiên hoặc tuần hoàn nước làm mát để làm cho miệng túi nguội nhanh chóng để tránh màng nhựa trong khu vực niêm phong bị quá nhiệt.
Cấu trúc của máy đóng gói chân không hai buồng
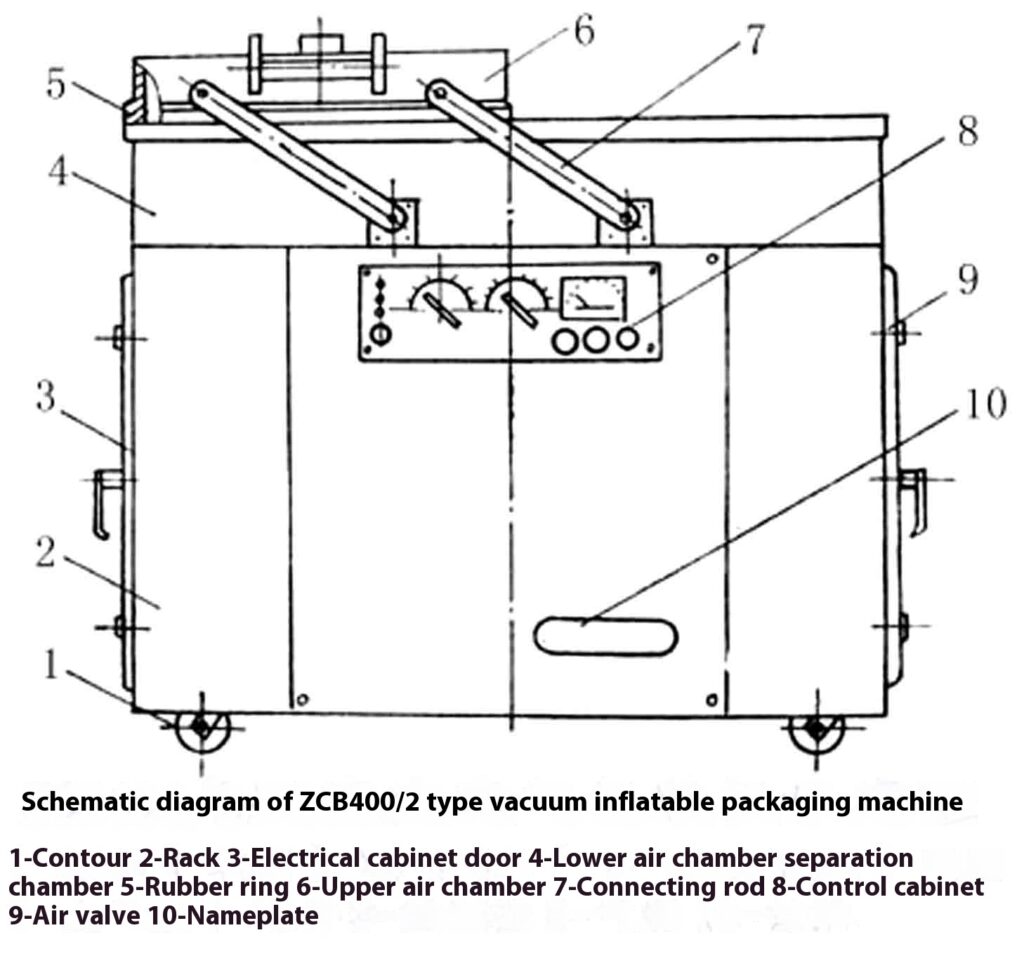
Phòng làm việc. Nó bao gồm một nắp trên và một đế dưới (buồng A và buồng B). Nắp trên và đế dưới được bịt kín bằng một vòng cao su.
Có hai khoang khí nhỏ ở phía trên nắp. Các khoang khí nhỏ được trang bị cơ chế gia nhiệt. Một đồng hồ đo chân không được lắp bên ngoài nắp, và cũng có các đầu nối gia nhiệt điện, ống khoang khí nhỏ và ống xả khoang khí. Các nắp trên và dưới được kết nối bằng một bộ liên kết bốn thanh để đảm bảo quay trơn tru.
Cơ chế gia nhiệt và niêm phong. Đầu gia nhiệt và nắp được kết nối bằng hai tấm đồng ở cả hai đầu. Hai khối đồng cố định ở cả hai đầu của đai gia nhiệt điện được cố định bằng vít để tránh tiếp xúc kém. Đầu gia nhiệt điện và nắp niêm phong được cách điện tuyệt đối để tránh đoản mạch.
Trong quá trình vận hành, buồng khí nhỏ và buồng khí lớn được hút chân không cùng lúc. Đầu gia nhiệt không hoạt động khi chênh lệch áp suất ở cả hai đầu là như nhau. Khi van khí của buồng khí nhỏ được kết nối với khí quyển để tạo ra chênh lệch áp suất, đầu gia nhiệt được ấn xuống, niêm phong được ấn và làm nóng cùng lúc. Thời gian và nhiệt độ gia nhiệt có thể được điều chỉnh. Hệ thống gia nhiệt là loại điều chỉnh áp suất, có thể sử dụng cho các vật liệu đóng gói khác nhau. Núm điều chỉnh được đặt trên bảng điều khiển máy. Đai gia nhiệt điện là đai hợp kim. Nghiêm cấm gia nhiệt không tải.
Căn cứ. Nó được chia thành hai khoang, A và B, với 16 vòi phun hơi ở cả hai bên. Có các miếng đệm sưởi ấm ở vị trí tương ứng của đầu sưởi ấm và một nhóm công tắc cam để chuyển đổi giữa các khoang A và B được đặt bên dưới.
Phần kết luận
Các loại túi đóng gói và máy đóng gói chân không là một phần không thể thiếu trong ngành thực phẩm và dược phẩm, đảm bảo chất lượng sản phẩm và kéo dài thời hạn sử dụng. Trong khi có nhiều loại túi khác nhau phù hợp với các vật liệu và tính thẩm mỹ khác nhau, máy đóng gói chân không tăng cường quá trình bảo quản bằng cách loại bỏ không khí, ngăn ngừa quá trình oxy hóa và tạo điều kiện cho quá trình khử trùng bằng nhiệt. Cấu trúc và nguyên lý hoạt động của cả máy đóng gói chân không một buồng và hai buồng đều đóng vai trò quan trọng trong việc hợp lý hóa quy trình đóng gói, giúp quy trình này hiệu quả hơn, đáng tin cậy hơn và phù hợp với nhiều loại sản phẩm. Việc hiểu các phương pháp đóng gói này là điều cần thiết để tối ưu hóa hoạt động đóng gói và đảm bảo sản phẩm được bảo vệ tốt khi lưu trữ và vận chuyển.
Đừng ngần ngại liên hệ với chúng tôi Bây giờ nếu bạn có bất kỳ câu hỏi nào.