Introduction
Small powder filling machines are specially designed to fill small containers with powdered products accurately and efficiently. They can be commonly seen in many different industries.
In the pharmaceutical industry, they are used to fill various powdered medicines. In the food industry, they are responsible for filling spices, powdered food additives and so on. And in the cosmetics industry, many powdered cosmetics are packaged by them. They are so precise when filling that the weights of the filled products can remain almost the same, which can minimize waste.
Moreover, these small powder filling machines are usually small in size and don’t take up much space. They are also easy to operate. Therefore, they are especially suitable for small-scale production factories or for use in laboratories. Aren’t they amazing!
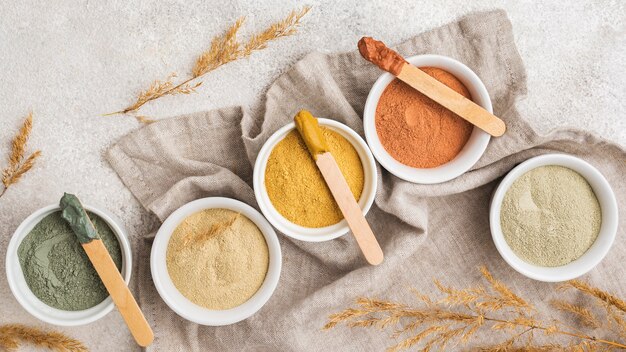
Benefits of Using a Small Powder Filling Machine
Precise and Efficient, Ensuring Quality
Small powder filling machines are just like amazing little helpers. They are equipped with advanced metering systems. These systems can fill powders into containers precisely, so that there won’t be much powder wasted and the quality of products can always be kept good. In places like pharmaceutical factories and food processing plants, the requirement for the amount of each portion of powder is very strict. At such times, the precision of small powder filling machines can play a big role.
Versatile and Capable of Handling Various Powders
They are really versatile little experts! Whether it’s very fine powder or coarse granules, they can handle them easily. With it, a factory can use just this one machine to fill many different products. In this way, there’s no need to buy many machines, which can save a lot of money. Moreover, with fewer machines on the production line, it’s also easier and more convenient to manage them.
Compact in Size, Occupying Little Space
Its body is designed to be compact and doesn’t take up much space. If the floor space in a factory is relatively small, it’s especially suitable. And it’s also very easy to integrate it into the existing production line without messing up the original production. It’s just like adding a new little member to the production line, and they can work together harmoniously.
Simple to Operate and Easy to Learn
This small powder filling machine is not complicated to use at all. It has clear operation buttons and display screens. Just like the simple games we play, workers can quickly master how to use it to fill powders after just a little learning. In this way, a lot of time won’t be wasted due to not knowing how to use the machine, and the production efficiency can be greatly improved.
Cost-effective and Helping to Reduce Costs
It can save money not only when being purchased but also when being used. Because it’s small in size, it consumes less electricity and is not easy to break down, so the maintenance cost is low. And because it can handle all kinds of powders, there’s no need to buy many machines with different functions. In this way, a lot of money can also be saved on the purchase of machines. For factories, it can save quite a lot of costs.
A Little Safety Guard, Ensuring a Safe Working Environment
It’s also a little safety guard. It has a special dust collection system and an enclosed chamber for filling. In this way, when filling powders, the powders are not easy to spill out, and workers won’t come into contact with those powders that may be hazardous. In this way, everyone can work in the factory in a healthier and safer way.
How to Choose the Right Small Powder Filling Machine for Your Needs
Selecting the ideal small powder filling machine is crucial for businesses seeking efficient and precise powder handling. Here are key factors to consider when making your choice:
1. Product Characteristics:
Determine the physical properties of your powder, including particle size, density, and flowability. These factors influence the type of filling mechanism and machine design required.
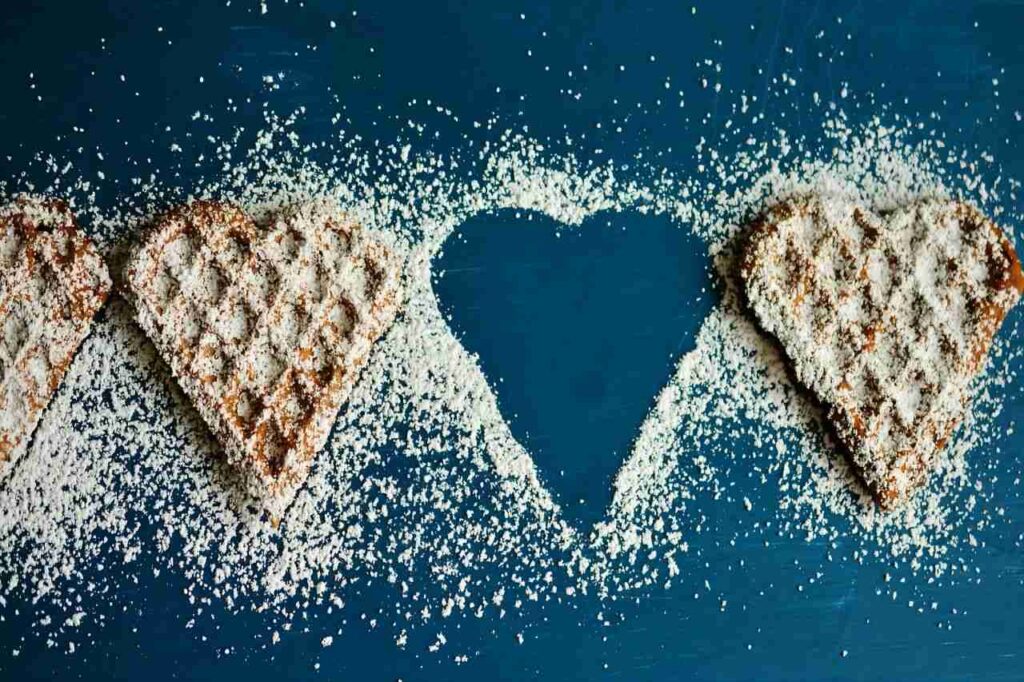
2. Filling Accuracy and Speed:
Establish the desired accuracy and speed of your filling process. Consider the tolerance levels required for your product and the production volume you aim to achieve.
3. Filling Range:
Identify the range of fill weights you need to accommodate. Ensure the machine can handle the minimum and maximum fill volumes required for your products.
4. Filling Mechanism:
Choose a filling mechanism that suits your powder’s characteristics. Auger fillers are suitable for free-flowing powders, while volumetric fillers are ideal for powders with poor flowability.
5. Machine Design:
Consider the machine’s overall design, including its size, weight, and ease of operation. Ensure it fits within your production space and can be integrated with your existing equipment.
6. Automation Level:
Determine the level of automation you require. Manual machines offer flexibility, while semi-automatic and fully automatic machines provide higher efficiency and consistency.
7. Cleaning and Maintenance:
Consider the ease of cleaning and maintenance of the machine. Regular cleaning is essential to prevent contamination and ensure optimal performance.
8. Safety Features:
Ensure the machine complies with industry safety standards and incorporates features such as guards, interlocks, and emergency stop buttons.
9. Manufacturer Reputation and Support:
Choose a reputable manufacturer with a proven track record and reliable customer support. This ensures access to technical assistance, spare parts, and software updates.
10. Cost and Return on Investment:
Evaluate the cost of the machine and its potential return on investment. Consider the long-term benefits of increased efficiency, reduced waste, and improved product quality.
Tips for Operating a Small Powder Filling Machine
Operating a small powder filling machine requires precision and attention to detail to ensure accurate and efficient filling. Here are some essential tips to guide you through the process:
Preparation:
Calibrate the machine:Before using the machine, calibrate it according to the manufacturer’s instructions to ensure accurate filling weights.
Clean the machine: Thoroughly clean the machine and all its components to prevent contamination and ensure proper operation.
Operation:
Load the powder: Fill the hopper with the powder to be filled. Ensure that the powder is free of lumps and foreign objects.
Set the filling parameters: Adjust the machine’s settings, such as fill weight, fill speed, and vibration intensity, to suit the specific powder and container.
Start the filling process: Initiate the filling cycle and monitor the machine’s operation closely.
Monitor the fill weight: Regularly check the filled containers to ensure they meet the desired weight specifications. Adjust the machine’s settings as needed.
Maintenance:
Clean the machine regularly: After each use, thoroughly clean the machine to remove any residual powder and prevent contamination.
Inspect the machine: Regularly inspect the machine for any signs of wear or damage. Replace worn or damaged parts promptly.
Lubricate the machine: Lubricate the machine’s moving parts according to the manufacturer’s instructions to ensure smooth operation.
Troubleshooting:
Inaccurate filling weights:Check the calibration of the machine, the fill weight settings, and the powder flow.
Powder bridging: Use a vibrator or anti-bridging device to prevent powder from clumping and blocking the filling nozzle.
Leaking: Inspect the seals and gaskets for damage or wear. Replace them if necessary.
Additional Tips:
Use a funnel: Use a funnel to guide the powder into the hopper and prevent spillage.
Handle the powder carefully: Avoid over-compacting the powder, as this can affect its flowability.
Store the powder properly: Store the powder in a dry and cool environment to prevent moisture absorption and clumping.
Troubleshooting Common Problems with Small Powder Filling Machines
Small powder filling machines are essential equipment in various industries, including pharmaceuticals, food, and cosmetics. However, like any machinery, they can encounter occasional problems that hinder their optimal performance. Understanding and addressing these issues promptly is crucial to maintain efficiency and prevent costly downtime.
One common problem is inconsistent filling accuracy. This can be caused by several factors, such as worn or damaged augers, improper calibration, or fluctuations in powder density. To resolve this, inspect the augers for wear and replace them if necessary. Calibrate the machine according to the manufacturer’s instructions and ensure that the powder density is consistent throughout the filling process.
Another issue is powder bridging, which occurs when powder particles form a cohesive mass that prevents them from flowing smoothly into the filling chamber. This can be addressed by using a powder conditioner to break up the agglomerates or by employing a vibrating hopper to promote powder flow.
Leaking powder is another common problem that can result from worn seals or gaskets. Inspect the seals and gaskets for damage and replace them if necessary. Additionally, ensure that the filling chamber is properly sealed to prevent powder from escaping.
Overfilling or underfilling can also occur due to incorrect machine settings or faulty sensors. Verify the machine’s settings and calibrate the sensors to ensure accurate filling. If the problem persists, consider replacing the sensors.
Electrical issues, such as power outages or faulty wiring, can also disrupt the machine’s operation. Check the power supply and wiring for any loose connections or damage. If necessary, contact a qualified electrician to resolve the issue.
In addition to these common problems, specific issues may arise depending on the type of powder being filled. For example, hygroscopic powders can absorb moisture from the air, leading to clumping and inconsistent filling. To prevent this, use a desiccant or moisture-proof packaging to keep the powder dry.
The Future of Small Powder Filling Machines
The packaging industry is constantly evolving, and with it, the demand for efficient and precise powder filling machines. Small powder filling machines, in particular, are gaining popularity due to their versatility and cost-effectiveness.
Current Trends
The current trend in small powder filling machines is towards automation and integration. Machines are becoming more sophisticated, with features such as automatic weight adjustment, real-time monitoring, and data logging. This allows for increased accuracy, reduced waste, and improved overall efficiency.
Emerging Technologies
Several emerging technologies are poised to revolutionize the small powder filling machine industry. These include:
Artificial Intelligence (AI): AI-powered machines can learn from historical data and make adjustments to optimize filling processes.
Internet of Things (IoT):IoT-enabled machines can connect to other devices and systems, allowing for remote monitoring and control.
3D Printing: 3D printing enables the rapid prototyping and production of custom-designed filling components.
Future Applications
The future of small powder filling machines lies in their expanded applications. These machines are expected to play a vital role in industries such as:
Pharmaceuticals: Precise filling of powders for capsules and tablets.
Food and Beverage: Packaging of powdered ingredients, spices, and supplements.
Cosmetics: Filling of powders for makeup, skincare, and hair care products.
Chemicals: Handling of hazardous and sensitive powders.
Conclusion
Small powder filling machines offer a cost-effective and efficient solution for filling small containers with powdered products. They are versatile, easy to operate, and can be customized to meet specific production requirements. By automating the filling process, these machines improve accuracy, reduce waste, and increase productivity. Their compact size and portability make them suitable for a wide range of applications, from small-scale manufacturing to laboratory research.
LTC Pack is a leading provider of equipment and services solutions for packaging beverage, food, home and personal care products in pouch, can, glass and other materials. With over 40,000 machines installed in more than 190 countries, we have nearly 20 years of proven experience, with a strong focus on the factory of tomorrow with advanced systems, line engineering and innovation. Our 500+ employees worldwide are passionate about providing solutions that fulfil customer needs and boost the performance of their lines, products and businesses. Delivering this level of performance requires that we stay flexible. We continuously ensure we understand our customers’ changing challenges and commit to meeting their unique performance and sustainability goals. We do this through dialogue and by understanding the needs of their markets, production and value chains. In turn, we apply our solid technical knowledge and smart data analytics to ensure lifetime productivity reaches its full potential. We call it Performance through Understanding.
A solution for every need. From packaging and blowing to filling, labelling and packing, through palletising, we have solutions designed to meet your any need.