Packaging materials include metal, plastic, glass, ceramic, paper, bamboo, wild mushrooms, natural fiber, chemical fiber, composite materials and other main packaging materials, and also include strapping, decoration, printing materials and other auxiliary materials. The specific material to be selected depends on the demand of the product, and environmental protection issues must also be considered.
Innovations in packaging materials include: pulp molding packaging materials for heat insulation, shockproof, impact-proof and perishable;
In design, strive to reduce the use of materials that are difficult to decompose in the later stage in packaging, and try to use materials that are light in weight, small in size, easy to crush or flatten, and easy to separate.
Type of Packaging Materials
Paper packaging materials: honeycomb paper for packaging paper, paper bag paper, desiccant packaging paper, honeycomb paperboard, kraft industrial paperboard, honeycomb paper core;
Plastic packaging materials: PP strapping tape, PET strapping tape, tear film, wrapping film, sealing tape, heat shrink film, plastic film, hollow board;
Composite soft packaging materials: soft packaging, aluminized film, iron core wire, aluminum foil composite film, vacuum aluminized paper, composite film, composite paper, BOPP;
Metal packaging materials: tinplate aluminum foil, barrel hoop, steel belt, strapping buckle, blister aluminum, PTP aluminum foil, aluminum plate, steel buckle;
Ceramic packaging materials: ceramic bottles, ceramic cylinders, ceramic jars, ceramic pots;
Glass packaging materials: glass bottles, glass jars, glass boxes;
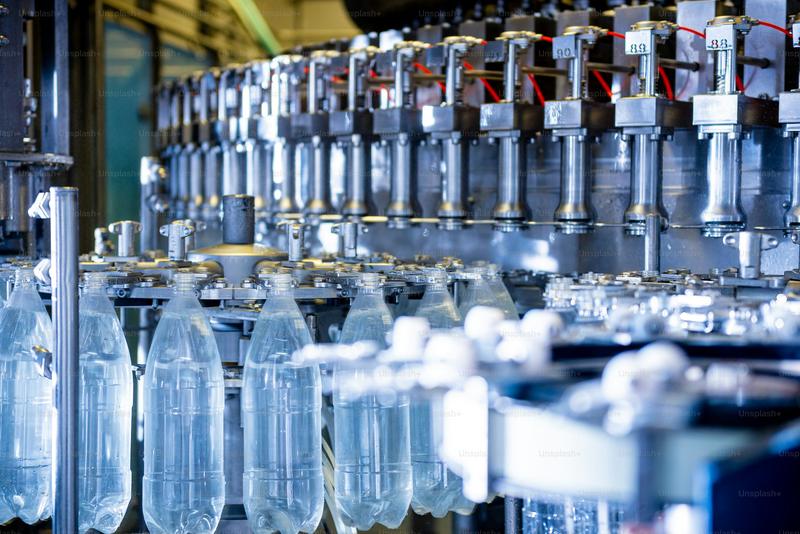
Wood packaging materials: packaging made of wood products and artificial wood boards (such as plywood, fiberboard), such as wooden boxes, wooden barrels, wooden boxes, wooden plywood, fiberboard boxes, plywood boxes and wooden pallets, etc.;
Other packaging materials/auxiliary materials:
Hot stamping materials: hot stamping materials, laser film, electrochemical aluminum hot stamping paper, hot stamping film, hot stamping film, hot stamping foil, hot stamping foil, color foil;
Adhesives, coatings: adhesive adhesives, composite adhesives, enhancers, starch adhesives, sealing glue, latex, resins, self-adhesives;
Packaging auxiliary materials: bottle cap glove machine, mold, gasket, handle, liner nozzle, sealing cap, packaging film.
Box Packaging For Cosmetic Product
Boxing refers to folding paper boxes or micro corrugated paper boxes made of two materials: cardboard and micro corrugated paperboard. The materials of packaging boxes can be divided into two categories: one is facial paper and the other is corrugated paper. Commonly used paper for packaging boxes include gray copper, single copper, white copper, gorgeous card, silver card, gold card, platinum card, laser card, etc.
“White background white board” refers to: white copper and single copper. The common point between white copper and single copper is that both sides are white. The difference is: “white copper” is smooth on one side and not smooth on the other side. In layman’s terms, the front side can be printed, but the back side cannot be printed; “single copper” has coated surfaces on both sides, and both sides can be printed. “Gray background gray board” has this kind of paper, but it is not used on packaging boxes; “gray background white board” is the so-called “gray copper paper”, that is, the front side is white and can be printed, and the back side is gray and cannot be printed. Generally, white card is also called “white background white board” paper, which is the abbreviation for general quotation (except special white cards, such as platinum card and silver card).
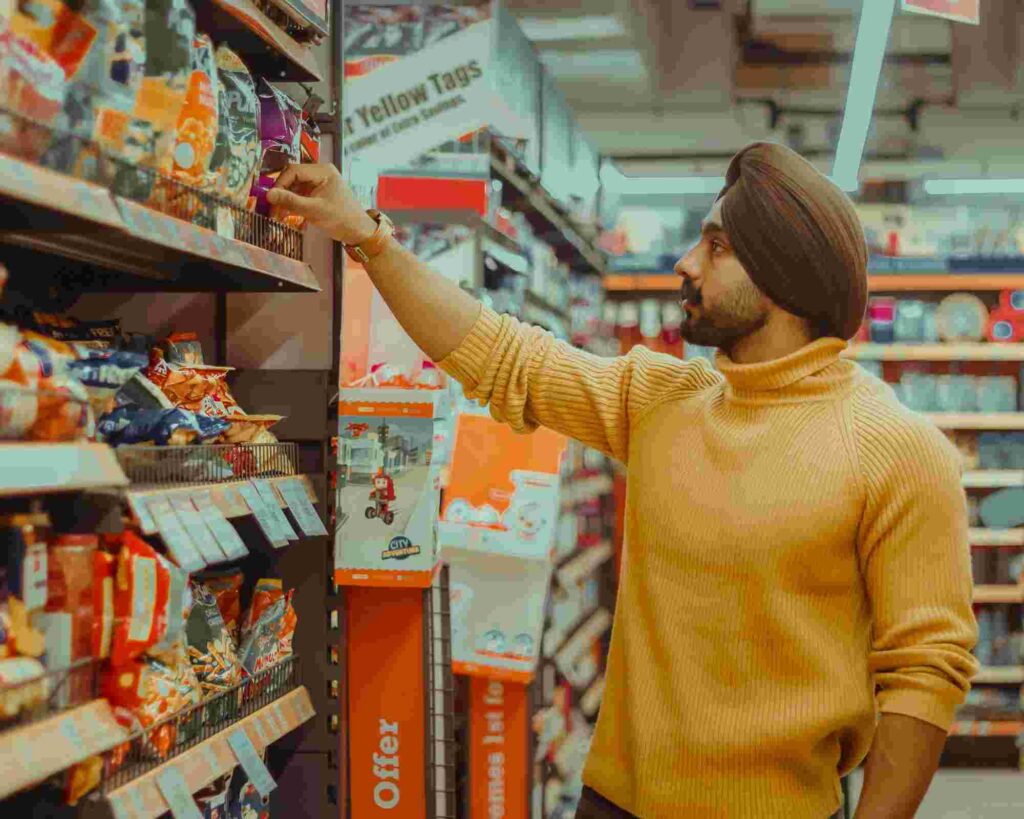
White cardboard, black cardboard
White cardboard has a wide range of applications, and is commonly used in cosmetic packaging, pharmaceutical packaging, cigarette packaging, wine packaging and food packaging. Its characteristics are that the overall paper material is firm and thick, the whiteness is high, the paper surface is smooth without rough spots, it is easy to print, the ink acceptability is good, and the glossiness is high. We usually choose this paper material first when printing cosmetic handbags. The reasons for choosing this paper material are: first, the paper is not easy to lose ink during printing, second, this kind of paper has good toughness, high folding resistance and is not easy to tear. Third, the paper has a high density. In addition to these advantages, white cardboard and black cardboard can be suitable for various surface treatment processes. Common production processes include lamination, varnishing, hot gold/hot silver, hot blue, red, green gold, convex, UV, embossing, etc. When making mask boxes, high white cardboard can also be die-cut into various required box structures to achieve the packaging effect desired by customers.
Gold cardboard, silver cardboard, laser gold card and various color gold cardboard
Gold and silver cardboard may be used more frequently in the mask packaging aspect, and there are many choices in the inner packaging of cosmetics, outer packaging boxes and daily toiletries packaging. Like toothpaste product packaging, health care products, medicine and gift box packaging. The biggest feature of gold and silver cardboard is that it looks more upscale, exquisite and classy visually. Gold and silver cardboard is a special paper. It is made by laminating a layer of gold and silver aluminum foil on white cardboard. The printing of gold-printed cardboard is slightly more complicated because of the material. Quick-drying printing ink is required during printing, and because the surface of gold and silver cardboard is easy to scratch, lamination protection is required in the subsequent process. After lamination, surface embossing, embossing, hot stamping, UV and other processes are performed. If gold and silver cardboard is used, the production cost will be slightly higher than that of ordinary white cardboard. However, in order to increase the sales and aesthetics of the product, using gold and silver cardboard or choosing other colors of gold cardboard may be a choice!
Kraft paper and special paper
The advantages of kraft paper are toughness, tear resistance and good waterproofness, but the surface is loose and a little rough. Most of the printing is single black. If the surface needs 4-color printing or spot color printing, the printing effect may be slightly worse than other paper printing because the paper itself is yellow. In the post-processing, if the hot stamping and UV are not performed without lamination, the hot stamping part will be incomplete or cannot be hot stamped because the surface of the paper itself is not smooth and delicate. The surface treatment process after lamination is better.
International big-name cosmetics boxes use special paper frequently. Special paper includes embossed paper with different texture ideas on the surface, glittering pearl paper with different colors, touch paper, colored corrugated paper, etc. Cosmetic boxes or packaging boxes made of special paper are very high-end. It can be printed in color, and can be directly hot stamped/hot stamped, embossed, etc. in the post-processing.
the general mask packaging box or cosmetic packaging box customization is mostly made of white cardboard and gold and silver cardboard, and the paper weight is selected at 350g or 400g. The box structure is mostly a plug box. According to the overall weight of the mask and the weight of the skin care product, the bottom can be improved. The bottom can be designed as a hook bottom box (glue at the bottom to increase the load-bearing capacity) or an automatic bottom box. In terms of packaging technology, white cardboard can be hot-stamped, UV, embossed, and concave and convex after lamination. Art paper can be directly screen-printed and hot-stamped. Gold cardboard can be hot-stamped, UV, embossed, and concave and convex after lamination.
Cosmetic packaging box production method and process
Cosmetic packaging can be divided into mid-range and high-end packaging. The production method and process of cosmetic packaging boxes must be inseparable from several common processes. In order to improve a higher grade, high-end cosmetic packaging will mostly choose some post-production processes or different box structures to enhance the overall visual effect and grade of the packaging and play an auxiliary role in increasing sales. However, no matter how things change, they still remain essentially the same. Any cosmetic packaging box or other product packaging or gift packaging must go through the following processes before it can be made. So what are their production procedures, methods and processes?
Printing
The first and most important step in cosmetic packaging is printing. The printing manufacturer uses offset printing (commonly known as color printing). Color printing is to print the desired color effect through the mixing of 4 primary colors, magenta, yellow, cyan, and black inks. Special gold, special silver, special red, etc. belong to the special color printing method. In addition to ordinary offset printing, the printing method needs to be adjusted under different conditions of the printing material. For example, various gold cardboard papers use UV printing. The more special colors in the design files provided by customers, the higher the printing cost will be. When printing cosmetic color boxes, printing gold and silver is also a printing effect to improve the upper grade. Before printing, the following processes need to be prepared. First, choose or design the box structure of the packaging paper box. Customers with samples can make it according to the customer’s samples. Why design the box structure first? Because there is a die-cutting process in the back process of the paper box, in order to make the box structure standard. Before designing, you can design the artwork according to the designed knife line. After designing and confirming the file, you need to make the plate first. Four-color printing is four screens, and one spot color is a spot color plate. The more spot colors, the more plates.
Process
After printing, surface treatment process is required. Among them, the most direct effect of laminating process and varnishing process is to protect the printing surface from scratches. They are a common production and processing process. For example, when making color boxes, when gray board paper is printed in a darker color, if it is not varnished, the entire surface will increase the dullness and old feeling, and the printed surface after varnishing will increase the overall glossiness, which will give people a brand new feeling visually. However, cosmetic packaging rarely uses varnishing process. More other processes such as laminating, hot stamping, hot silver, UV, convex and concave, embossing, etc. are used to increase the high-end and exquisiteness of the packaging products.
Die-cutting
Die-cutting is a necessary process before pasting boxes. The box structure selected before designing the artwork is made into a knife plate. When die-cutting, the knife plate is installed on the die-cutting machine. After the professional die-cutting master aligns the position and corners, it is die-cut into an unfolded shape according to the shape of the knife plate. The size deviation of die-cutting is about 1 mm, which is within the normal range.
Pasting boxes
The useless edges and corners have been removed from the printed surface after die-cutting. The next step is to paste the box into shape. When pasting the box, it is necessary to carefully align the line position. If there are high and low lines (upper and lower lines are not aligned) and flares (the pasting line exceeds the pasting position line), they are all unqualified products. Manufacturers will conduct random inspections on products when pasting boxes. Qualified products can be packed and sent to customers for use.
Through the above understanding, when we need to customize cosmetic packaging boxes, we first choose commonly used paper materials, such as: high white cardboard, various gold cards, silver cards or laser cardboard, and special paper with different pressure textures of cow cardboard. The weight used is generally 350 grams. Then choose the post-production process. The common production methods are: white cardboard is coated with matte film and then hot stamped with gold/silver/laser on the surface and combined with embossing technology to emboss the logo or other patterns. Gold cardboard must be coated before surface UV treatment. General art paper can be directly UV or coated and then hot stamped or other processes with different requirements. The specific process procedures can be made according to customer customization requirements. The box type usually uses a plug box. Lock bottom box and hook bottom box are also common. Airplane box can be used for gift packaging or a whole set of cosmetic packaging. It is recommended to hold lightweight cosmetics.
Automatic Packaging Machine for Cosmetic
Automatic packaging machines are crucial in the cosmetic industry, as they streamline production processes and enhance efficiency. These machines are designed to handle various packaging tasks, from filling to sealing, labeling, and even boxing. They ensure consistency, speed, and precision, which are essential for large-scale production. Below are some types of automatic packaging machines used in the cosmetic industry:
1. Filling Machines
Filling machines are designed to accurately fill containers with cosmetic products like creams, lotions, shampoos, or serums. These machines can be:
- Volumetric Fillers: Used for liquids and semi-viscous products.
- Piston Fillers: Ideal for more viscous products, like creams and gels.
- Pump Fillers: Suitable for thin to medium viscosity liquids.
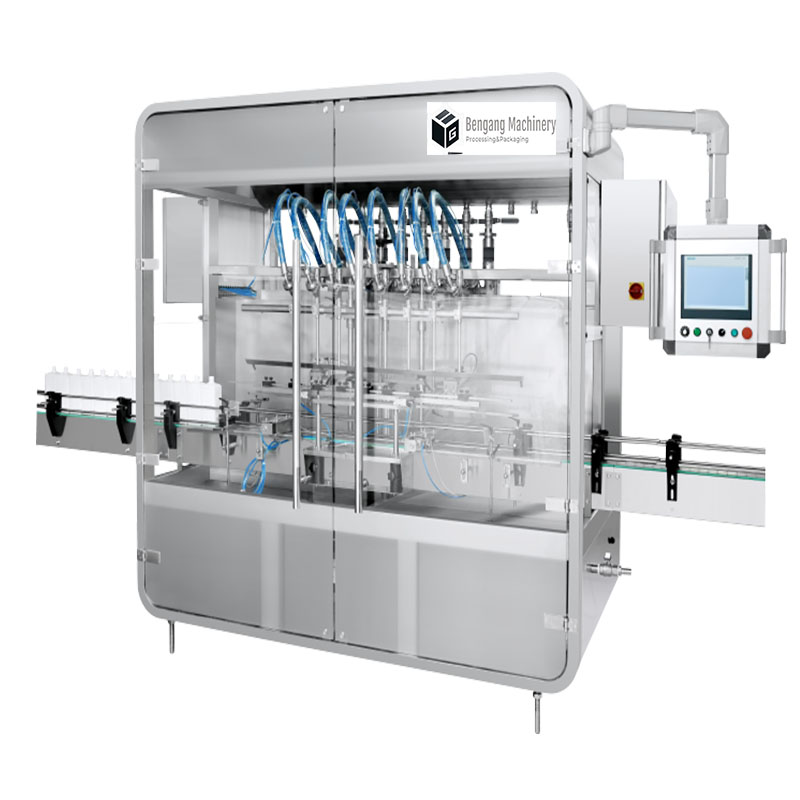
2. Sealing Machines
Sealing machines ensure that the cosmetic product’s container is tightly closed, preventing leakage and contamination. Common types of sealing machines include:
- Heat Sealing Machines: Used for sealing plastic packaging, typically used in sachets or pouches.
- Cap Sealing Machines: Automatically screw or press caps onto bottles or jars, ensuring a tight seal.
3. Labeling Machines
Labeling machines are essential for applying labels to cosmetic containers. They can handle a wide range of labeling tasks, from applying labels to bottles, jars, and tubes to providing high-quality graphics and barcodes. Types of labeling machines include:
- Wrap-Around Labeling Machines: For bottles and cylindrical products.
- Top and Bottom Labeling Machines: Used for rectangular packaging like boxes or jars.
- Custom Labeling: Machines can also accommodate special label designs, ensuring brands’ logos are prominently displayed.
4. Cartoning Machines
Cartoning machines are designed to place cosmetic products into cartons or boxes. They can be customized to handle products like skincare bottles, makeup kits, and perfume boxes. These machines are efficient in folding, sealing, and applying glue to cartons. They can be integrated with other packaging lines for seamless production.
5. Shrink Wrapping Machines
Shrink-wrapping machines are widely used in the cosmetic industry for packaging multi-product sets or ensuring tamper-evident packaging. The product is placed in a shrink film sleeve, which is then heated to tightly fit around the product.
6. Palletizing Machines
After products are packaged, they are ready for shipment. Palletizing machines automate the process of stacking boxes onto pallets, which helps improve efficiency and reduce the risk of manual handling injuries. These machines are ideal for high-volume cosmetic production.
Benefits of Automatic Packaging Machines for Cosmetics:
- Efficiency: Automatic machines work faster and consistently, leading to higher throughput in packaging operations.
- Accuracy: These machines ensure that each step in the process, such as filling, sealing, and labeling, is done with precision.
- Cost-Effective: While the initial investment in automatic machines can be high, the reduction in labor costs and the increase in productivity make them cost-effective over time.
- Customization: Modern packaging machines can be customized to meet specific needs, such as packaging different sizes, shapes, and types of cosmetic products.
- Hygiene: Automated systems minimize human contact with products, helping to maintain a high level of hygiene and reducing the risk of contamination.
Conclusion
Cosmetic packaging plays a critical role in enhancing the aesthetic appeal, protecting the product, and ensuring the safety and quality of cosmetics. As the demand for innovative, sustainable, and efficient packaging continues to grow, brands must stay ahead of the curve by selecting the right materials and packaging technologies.
By choosing the appropriate packaging materials, such as white cardboard, gold or silver cardboards, and special papers, along with post-production techniques like hot stamping, UV treatment, and embossing, brands can create premium and visually appealing packaging that stands out on the shelves. Furthermore, the integration of automatic packaging machines helps streamline production processes, ensuring speed, precision, and cost-efficiency.
In an industry driven by consumer preferences, sustainability, and creativity, understanding the full scope of cosmetic packaging materials, processes, and automated machinery is essential for building a successful brand. With the right balance of materials, design, and automation, cosmetic brands can not only protect and present their products beautifully but also meet the growing expectations of eco-conscious consumers.