Introduction
Heat sealing is a vital process in the packaging industry, used to bond plastic films through heat and pressure. Different methods of heat sealing offer distinct advantages based on the type of material and the specific packaging needs. Whether you’re sealing polyethylene films, composite materials, or specialized films for sensitive products, selecting the right heat sealing method can ensure strong, durable seals that maintain product integrity. This guide explores the most common heat sealing methods, including plate, roller, pulse, and ultrasonic sealing, along with their applications and benefits in packaging.
According to the different heating and pressurizing methods, the heat sealing methods of heat-sealing machines can be divided into the following types.
Plate heat sealing
Plate heat sealing is the most common heat sealing method. It uses a heating plate to intermittently heat and pressurize to achieve the sealing of plastic film. The heat sealing principle is shown in Figure 6-2. The two layers of film 3 to be sealed are transported between the heating plate 1 and the workbench 5, and then pressed tightly against the anti-sticking material 4. The heating plate 1 and the workbench 5 heated to a certain temperature (constant temperature control) are heated and pressurized, and then cooled to achieve a tight seal.
Commonly used anti-sticking materials are high-temperature resistant polytetrafluoroethylene or glass cloth, mainly to avoid the adhesion of the T-table and the film material layer, so that the bag mouth is beautifully sealed and the workbench can be kept clean. The electric heating wire 2 installed in the heating plate 1 heats the heating plate. The heating temperature is usually detected by a resistive temperature measuring element and displayed by a temperature display instrument. The temperature is adjusted by a voltage regulator or a resistor device. To ensure high-quality sealing seams, the heat-sealing surface of the heating plate should be flat, and the supporting plane should be flat or padded with a heat-resistant rubber cushion. The heat-sealing pressurizing movement mechanism of the heating plate 1 can be pneumatic, hydraulic, cam, electromagnetic, etc.
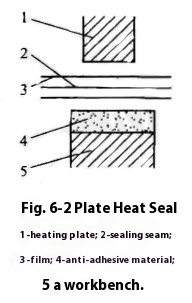
This hot-melt sealing device in the form of a slat structure has a simple structure and principle, and a fast sealing speed. It is widely used in intermittent automatic packaging machines. It is mainly used for heat sealing of polyethylene films and polyethylene composite films, but not for heat sealing of films that are easily shrunk or decomposed by heat.
Roller heat sealing
Roller heat sealing is to seal the plastic film by applying pressure with a continuously rotating roller and heating with one or two rollers in a pair of rollers.
The principle of roller heat sealing is shown in Figure 6-3. When the two layers of film 2 to be sealed are pulled through a pair of heating rollers 1 (or only one heating roller), they are heated and pressurized, and then cooled to achieve a tight seal. The resistance heater is set in the heating roller, and the current is transmitted to the heating wire through the wiring device (such as brushes, slip rings and wires) insulated from the machine. The device for adjusting the temperature and the device and instrument for detecting and displaying the temperature of the heat sealing roller are set outside.
The characteristic of roller heat sealing is continuous sealing, which is suitable for heat sealing of composite films composed of base film (cellophane) and heat-sealing film (polyethylene); in some continuous automatic packaging machines with multiple functions such as bag making, filling and sealing, the heat sealing roller can not only complete the longitudinal heat sealing of the bag making packaging film material, but also play the role of pulling and conveying the packaging film material belt. As for single film, it is easy to deform due to heat, which will affect the sealing quality, so it is not suitable to use.
Belt heat sealing
As shown in Figure 6-4, it sandwiches the two layers of film 2 between a pair of circular thin belts 1 (such as polytetraethylene belt, steel belt, stainless steel belt or nylon textile belt) rotating in opposite directions, and heats them at the heating parts 4 set on both sides of the ring belt to make the two layers of film between the ring belts bonded, and then cold presses at the cooling part 5 to seal the film 2. Before the seal is completely formed, the seal is embossed by a pair of embossing wheels with pre-adjusted pressure, and then the production date is printed by the printing code wheel, and finally the seal is completed.
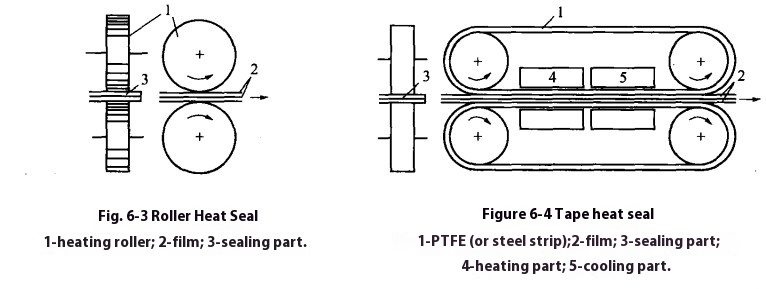
This method is suitable for heat sealing of composite film materials. Even films that are easy to deform can be continuously heat-sealed using this machine, and the sealing speed is relatively high, so it is widely used.
Sliding Roller Heat Sealing
As shown in Figure 6-5, the two overlapping layers of film 1 are passed between a pair of heating plates 4 to be heated to a softened and molten state, and when passing between the closely pressed heat sealing roller wheels 3, they are squeezed and welded. The characteristics of this type of sealing device are that the resistance heater and the heat sealing roller wheel are each independent components, which simplifies the roller wheel structure. The overall structure is simple and has a wide range of applications.
This method can be applied to the continuous heat sealing of film packaging materials, and can also be used for continuous heat sealing of films with large thermal deformation. If the machine stops unexpectedly, the film material between the electric heating plates will be overheated and lost, so the heater is required to be able to evacuate automatically to avoid overheating of the film.
Sliding Heat Sealing
Sliding heat sealing is used for wrapping packaging, as shown in Figure 6-6. It uses a film 3 to wrap the packaged object 2, so that it slides on the heating plate 4, and relies on the slight pressure applied by the packaged object and the heat of the heating plate 4 to bond the overlapping parts of the two layers of film.
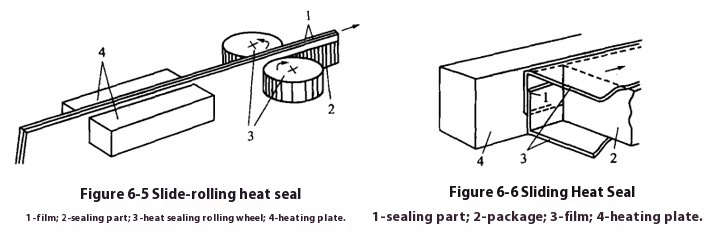
Pulse heat sealing
As shown in Figure 6-7, the nickel-chromium alloy strip 2 presses the film 4 onto the heat-resistant rubber 5, and the nickel-chromium alloy strip 2 is instantly heated by a large current, and the heat is used for heat sealing. Its characteristic is that the alloy strip 2 leaves the heat-sealed part only after cooling, so even films that are easily deformed can be heat-sealed using this method. This method is suitable for sealing products with high requirements for sealing strength and sealing, such as liquid packaging and vacuum packaging. This method is generally suitable for intermittent sealing and is widely used in bag making machines or automatic packaging machines.
Melt-cut heat sealing
As shown in Figure 6-8, the heating knife 5 (or steel wire) is used to melt and cut the film 2 and seal it at the same time. This sealing mechanism has a simple structure, fast sealing speed, and can simultaneously complete the melting and cutting and sealing of the film. However, due to the limitation of the weld joint area, the sealing strength is relatively small and it is easy to open. It is only suitable for inner packaging of small quantities of fine powder and granular items.
Pulse melting heat sealing
The melting heat sealing requires frequent heating of the blade and steel wire, while the pulse cutting heat sealing is the opposite, as shown in Figure 6-9. When the pressure plate 6 drives the cast alloy wire 1 to press the film 2 onto the heat-resistant rubber 3, the nickel-chromium alloy wire 1 is instantly energized and continues to press the heated and melted sealing part until it is released after cooling. This method can also complete the melting and sealing of the film at the same time.
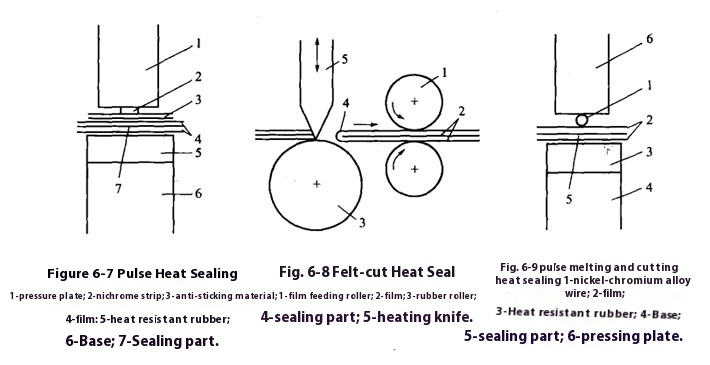
Melting heat sealing
As shown in Figure 6-10, it is to bring the heating plate 1 or the flame close to one end of the superimposed film 4 to melt and bond them. This method can make the heat-shrinkable biaxially oriented polypropylene film have a strong sealing strength.
Ultrasonic heat sealing
As shown in Figure 6-11, this heat sealing mechanism is composed of a high-frequency oscillator, a magnetostrictive vibrator 1 that converts high-frequency electrical energy into longitudinal vibration, and an exponential curve amplitude amplifier 2 that transmits the longitudinal vibration to the film. During heat sealing, the ultrasonic vibration transmitted by the exponential curve amplitude amplifier causes the overlapping surface of the film 4 to heat up and melt and bond.
This sealing method is characterized by heat generation at the center of the film overlap, which is suitable for continuous sealing of films that are easily shrunk by heat, such as biaxially stretched films. It can heat seal a variety of plastic film materials (such as polypropylene, nylon, aluminum-plastic composite materials, polyoxyethylene cans, etc.), and can be well sealed even if the packaging material is accidentally contaminated by water, oil, etc. during material filling. It also has high sealing quality for plastics that are prone to heat shrinkage deformation or thermal decomposition. It is particularly suitable for heat sealing in the packaging of food, medicine, radio and electronic components that are sensitive to thermal radiation, and is widely used in bag making machines or automatic packaging machines.
High-frequency heat sealing
As shown in Figure 6-12, high-frequency heat sealing is to press the film 4 with a high-frequency electrode 2, add a high-frequency voltage, and heat-seal by the dielectric loss of the polymer. The temperature of the sealing part is the highest at the sealing surface, so the film will not overheat and the sealing strength is high.
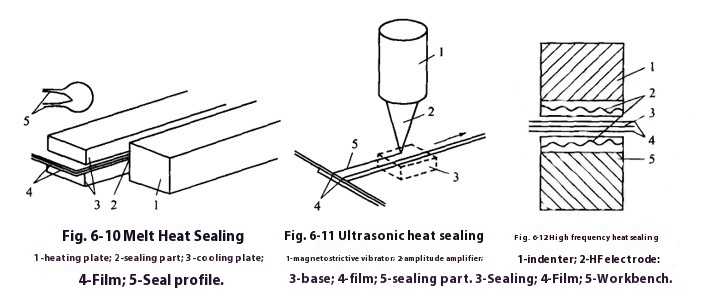
The heat sealing time of the heat press sealer is related to the heating temperature, heating method, film material, film material thickness and sealing pressure. For film materials of the same material and thickness, when the sealing pressure is constant, the higher the heating temperature, the shorter the heat sealing time. Heat sealing heating temperature, pressure, time and other parameters should be determined by experimental methods based on the mechanical and physical properties of the sealed material.
Conclusion
A heat-sealing machine is a machine that seals packaging containers by heat sealing. It is widely used for heat sealing of various plastic bags. Understanding the variety of heat sealing methods—from the simplicity of plate heat sealing to the advanced capabilities of ultrasonic sealing—enables manufacturers to select the most efficient and suitable solution for their packaging needs. Each sealing method offers specific advantages based on the materials, production speed, and quality required. By choosing the right technique, companies can improve packaging efficiency, reduce waste, and ensure high-quality seals that meet industry standards.